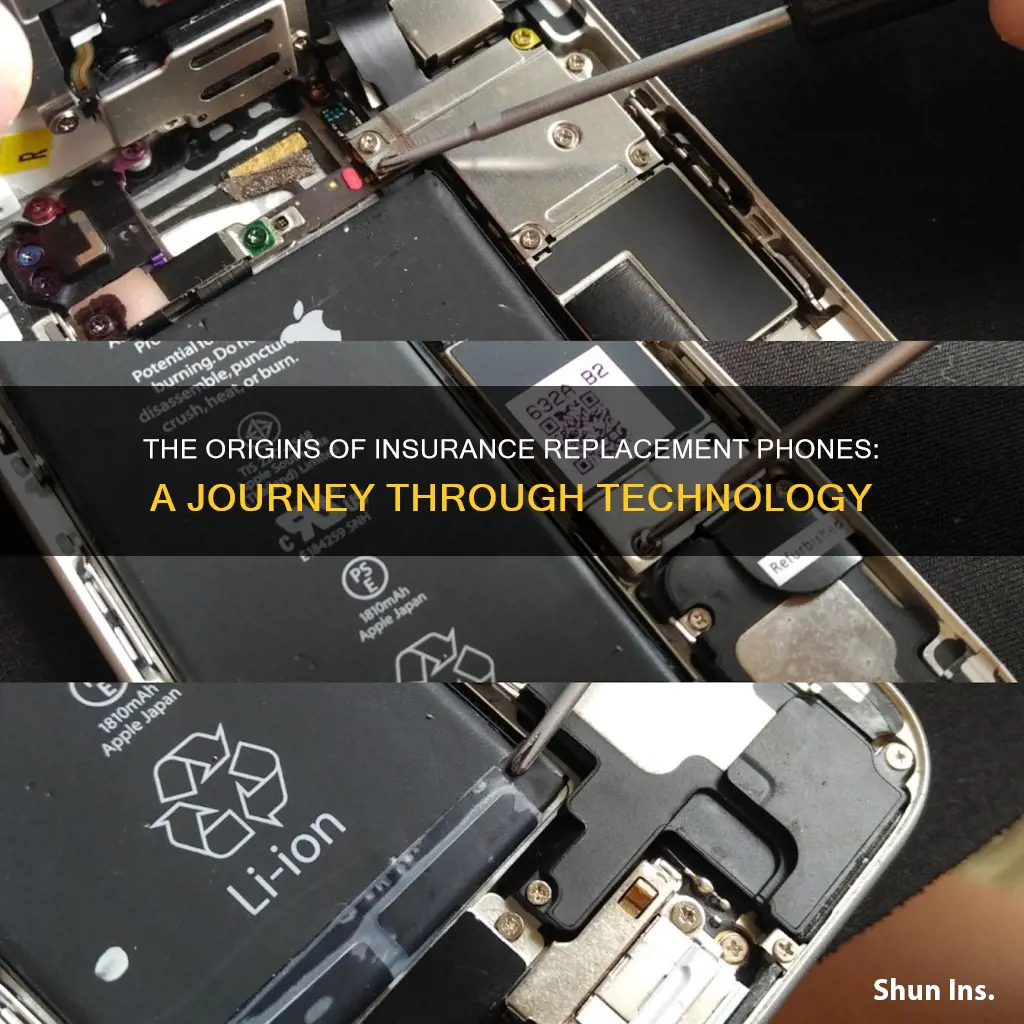
The insurance replacement phone is a device provided by insurance companies to customers whose phones have been damaged or lost. This service ensures that policyholders can maintain their communication and access to essential services without incurring significant costs. The origin of these replacement phones can be traced back to the insurance industry's efforts to offer a seamless and efficient solution for customers, often in partnership with phone manufacturers or retailers. The process typically involves the insurance company assessing the damage or loss, approving a replacement, and arranging for the delivery of a new device, which may be a similar model to the original or a newer version, depending on the insurance provider's policies and the customer's preferences.
What You'll Learn
- Manufacturing Process: From raw materials to assembly line production
- Supplier Networks: Identifying and sourcing components for phone production
- Quality Control: Ensuring devices meet standards before replacement
- Distribution Channels: How phones are transported to insurance companies
- Customer Service: Handling claims and providing support for replacement phones
Manufacturing Process: From raw materials to assembly line production
The process of manufacturing insurance replacement phones involves a series of intricate steps, starting with the selection of raw materials and ending with the final assembly. This journey ensures that each device is not only functional but also meets the required quality standards. Here's an overview of the manufacturing process:
Raw Material Selection: The foundation of any electronic device lies in its raw materials. For insurance replacement phones, manufacturers typically use a combination of metals, plastics, and glass. The most common materials include aluminum or stainless steel for the frame, providing durability and strength. Plastic, often in the form of polycarbonate or ABS, is used for the back cover and sides, offering a lightweight yet sturdy structure. Glass, usually Gorilla Glass or a similar durable variant, is employed for the display screen, ensuring scratch resistance and visual clarity. These materials are carefully sourced to meet the industry's highest standards.
Component Manufacturing: Once the raw materials are acquired, the manufacturing process begins with the production of individual components. This stage involves precision engineering and specialized machinery. For instance, the display screen is crafted from glass sheets, which are cut, polished, and treated to enhance durability. The circuit board, a critical component, is manufactured using printed circuit board (PCB) technology, where intricate circuits and connections are etched onto a substrate. Other components like the processor, memory chips, and sensors are also produced, each requiring specific manufacturing techniques to ensure optimal performance.
Assembly: The assembly line is where the various components come together to form a complete phone. This process is highly automated and involves multiple stages. Firstly, the frame is constructed by welding or soldering the metal parts, ensuring a sturdy structure. The display screen is then carefully attached to the frame, often using automated precision tools. Next, the circuit board is inserted, and all the electronic components are soldered into place. The back cover and sides are snapped into the frame, and the battery is installed. Quality control checks are performed at each step to ensure the phone's integrity.
Final Testing and Quality Assurance: After the assembly is complete, the phones undergo rigorous testing to ensure they meet the required specifications. This includes functional tests to check the performance of various features, such as the camera, touch screen, and connectivity. Battery life, signal strength, and overall device stability are also evaluated. Additionally, cosmetic inspections are conducted to ensure the phone's appearance is flawless. Any device that fails to meet these standards is returned to the assembly line for adjustments or discarded, ensuring only the highest-quality products reach the market.
The manufacturing process of insurance replacement phones is a complex and meticulous journey, requiring skilled labor and advanced technology. From the selection of raw materials to the final assembly and quality assurance, each step contributes to the creation of a reliable and functional device, ready to serve its purpose in the market.
Juggling Multiple Policies: Navigating Short-Term Insurance Overlap with New Coverage
You may want to see also
Supplier Networks: Identifying and sourcing components for phone production
The insurance replacement phones you see being offered as a service are often sourced from various suppliers and manufacturers who specialize in producing devices for the mobile phone market. These phones are typically designed and manufactured to meet specific standards and specifications set by the insurance companies or the device manufacturers themselves. The process of identifying and sourcing components for phone production involves a network of suppliers and a well-organized supply chain.
Supplier networks play a crucial role in the production of these replacement phones. Here's an overview of how it works:
Supplier Identification: The first step is to identify reliable suppliers who can provide the necessary components and parts. This involves researching and evaluating potential suppliers based on their reputation, quality standards, and ability to meet production requirements. Insurance companies or phone manufacturers often have a list of approved suppliers or engage in a competitive bidding process to select the best partners.
Component Sourcing: Once the suppliers are identified, the sourcing of components begins. This includes microprocessors, displays, batteries, cameras, and other essential parts. Each component has its own set of specifications and requirements, and suppliers must ensure they meet these standards. For example, the processor might need to be compatible with the latest operating system, and the display should have a specific resolution and refresh rate.
Quality Control: Sourcing components is just the beginning. Stringent quality control measures are implemented to ensure that the phones meet the required standards. This involves testing each component and the assembled phone for performance, durability, and reliability. Quality assurance teams inspect the devices for any defects or deviations from the specifications.
Assembly and Production: After sourcing and quality control, the components are assembled to create the final product. This step involves skilled labor and specialized equipment to ensure precision and efficiency. The assembly process is carefully managed to maintain consistency and meet production targets.
Logistics and Distribution: Once the phones are assembled, efficient logistics and distribution networks come into play. These networks ensure that the replacement phones are delivered to the insurance companies or directly to the customers in a timely manner. Proper inventory management and transportation systems are crucial to handle the volume and ensure customer satisfaction.
Supplier networks and efficient sourcing are vital to the entire process, allowing insurance replacement phone services to provide customers with reliable devices when their phones are damaged or lost. This network-based approach ensures a steady supply of components and phones, catering to the demands of the insurance industry and consumers.
Name Change and Insurance: Navigating the Process in America
You may want to see also
Quality Control: Ensuring devices meet standards before replacement
The process of obtaining insurance replacement phones involves a meticulous quality control system to ensure that the devices meet the necessary standards and provide a seamless experience for customers. This quality control process is crucial to maintain customer satisfaction and trust in the insurance provider's services. Here's an overview of how this quality control is implemented:
Device Inspection and Testing: When a damaged or faulty device is reported to the insurance company, the first step is to thoroughly inspect and assess the device. This inspection includes checking for physical damage, such as cracked screens, water damage indicators, or any visible signs of tampering. Advanced testing methods are employed to evaluate the device's performance, including stress tests, battery health checks, and software diagnostics. These tests ensure that the device functions optimally and meets the required specifications.
Standardized Replacement Criteria: Insurance companies have established strict replacement criteria to ensure that the replacement phones are of high quality. These criteria often include guidelines on the age and model of the device, ensuring that the replacement is appropriate for the customer's needs. For instance, an insurance provider might offer a newer model of the same brand or a similar device with comparable features to the original. This standardization helps in maintaining a consistent level of quality across all replacement phones.
Supplier and Manufacturer Collaboration: To ensure the highest quality, insurance companies often collaborate closely with device manufacturers and authorized suppliers. These partners provide replacement devices that meet the specified standards. The insurance provider's quality control team works with manufacturers to establish a seamless process for device sourcing, packaging, and distribution. This collaboration ensures that the replacement phones are authentic, properly configured, and ready for immediate use upon delivery.
Quality Assurance Protocols: Implementing rigorous quality assurance protocols is essential. This includes random sampling and testing of replacement devices during the manufacturing process. Advanced quality control software can be utilized to scan devices for any defects or performance issues. By employing these measures, insurance companies can identify and rectify any potential problems before the devices reach customers, ensuring a positive user experience.
Customer Feedback and Continuous Improvement: Feedback from customers is an integral part of the quality control process. Insurance companies encourage customers to provide feedback on their replacement devices, including any issues encountered. This feedback is then analyzed to identify areas for improvement. Continuous monitoring and adjustments to the quality control process ensure that the insurance provider can adapt to changing industry standards and customer expectations.
Haven Insurance Phone: Contacting Your Guardian Angel
You may want to see also
Distribution Channels: How phones are transported to insurance companies
The process of obtaining and distributing replacement phones to insurance companies is a well-established system, often involving a network of authorized dealers and manufacturers. When a customer files a claim with their insurance provider, the company typically initiates the process of acquiring a replacement device. This is where the concept of 'distribution channels' comes into play, ensuring a seamless flow of products from the manufacturer to the insurance company.
The first step in this distribution channel is the selection of a reputable dealer or retailer who has a direct relationship with the phone manufacturer. These dealers often have exclusive agreements, allowing them to purchase devices at a discounted rate. Once the insurance company places an order, the dealer arranges the purchase and ensures the phones are in stock or sourced from the manufacturer's inventory. This initial stage is crucial as it sets the foundation for a timely and efficient delivery.
Transportation and logistics play a vital role in the next phase. The dealer, or in some cases, the insurance company itself, arranges for the phones to be transported to the designated location. This could be a regional distribution center or a specific address provided by the insurance company. Efficient logistics management is essential to ensure the phones arrive in good condition and on time, especially when dealing with large volumes of devices. Specialized shipping companies or carriers with experience in handling electronic goods are often employed for this task.
Upon arrival at the insurance company's facility, the phones undergo a quality check to ensure they meet the required standards. This step is critical to maintain customer satisfaction and the insurance company's reputation. After the inspection, the devices are stored, ready to be dispatched to the policyholder. The insurance provider then arranges the final leg of the journey, delivering the replacement phone directly to the customer's specified address.
In summary, the distribution channels for insurance replacement phones involve a carefully orchestrated process, starting from authorized dealers and manufacturers to efficient transportation and quality control. This system ensures that insurance companies can promptly provide replacement devices to their customers, maintaining a positive relationship and trust in the insurance service.
Life Events: Insurance Enrollment Explained
You may want to see also
Customer Service: Handling claims and providing support for replacement phones
When a customer's phone is damaged or lost, insurance companies often provide a replacement device to ensure their policyholders can continue using their services. This process involves a careful and efficient handling of claims to maintain customer satisfaction. Here's a step-by-step guide on how customer service teams can effectively manage these replacement phone claims:
Upon receiving a claim, the customer service representative should first verify the details. This includes confirming the policy coverage, the extent of the damage or loss, and the customer's eligibility for a replacement. It is crucial to ask for necessary documentation, such as proof of purchase, insurance policy details, and any relevant reports from the incident. By doing so, the company can ensure that the claim is legitimate and falls under the insurance coverage.
Once the claim is approved, the representative should promptly initiate the replacement process. This involves contacting the insurance provider's network of authorized repair centers or retailers. The goal is to source a replacement phone that matches the customer's original device in terms of model, color, and storage capacity, if possible. Providing the customer with an estimated timeline for the replacement phone's arrival is essential to manage expectations.
During the replacement process, regular updates should be provided to the customer. This can be done via email or text messages, keeping them informed about the status of their claim. If there are any delays or issues, the customer service team should proactively reach out to explain the situation and offer potential solutions. Quick response times and transparent communication are key to maintaining a positive customer experience.
After the replacement phone is delivered, the customer service representative should conduct a thorough inspection to ensure the device is in good working condition. This step is vital to prevent any potential issues from arising later. If everything is in order, the customer should be guided through the setup process, ensuring they can use their new phone immediately. Finally, a follow-up call or survey can be conducted to gather feedback and ensure the customer's satisfaction with the entire process.
In summary, handling insurance replacement phone claims requires a well-organized and customer-centric approach. By efficiently verifying claims, initiating replacements, and providing regular updates, customer service teams can ensure a smooth experience for policyholders. Prompt issue resolution and transparent communication are essential to building trust and maintaining a positive relationship with the customers.
Specialty Doctors: Insurance Coverage Explained
You may want to see also
Frequently asked questions
Insurance companies typically partner with authorized dealers or retailers who specialize in mobile devices. These partners have agreements with manufacturers or wholesalers to source the specific models required for replacements.
In most cases, customers do not have the option to select the exact model. Insurance companies usually provide a list of approved devices that meet certain criteria, such as being within a specific price range or having similar features to the original phone.
Reputable insurance companies maintain strict quality control measures. They often work with trusted suppliers who adhere to industry standards and offer warranties or guarantees on the devices they provide.
Insurance replacement phones can be either brand new or refurbished, depending on the company's policies and the customer's preferences. Some insurers may offer a choice between new and refurbished options, while others might default to refurbished devices to reduce costs.
In such cases, the customer can usually request an alternative device within the approved list. Insurance companies may accommodate these requests, but it might require additional documentation or verification to ensure the new device meets the required specifications.